The 7 Role of QC Testing in Flash Storage Manufacturing
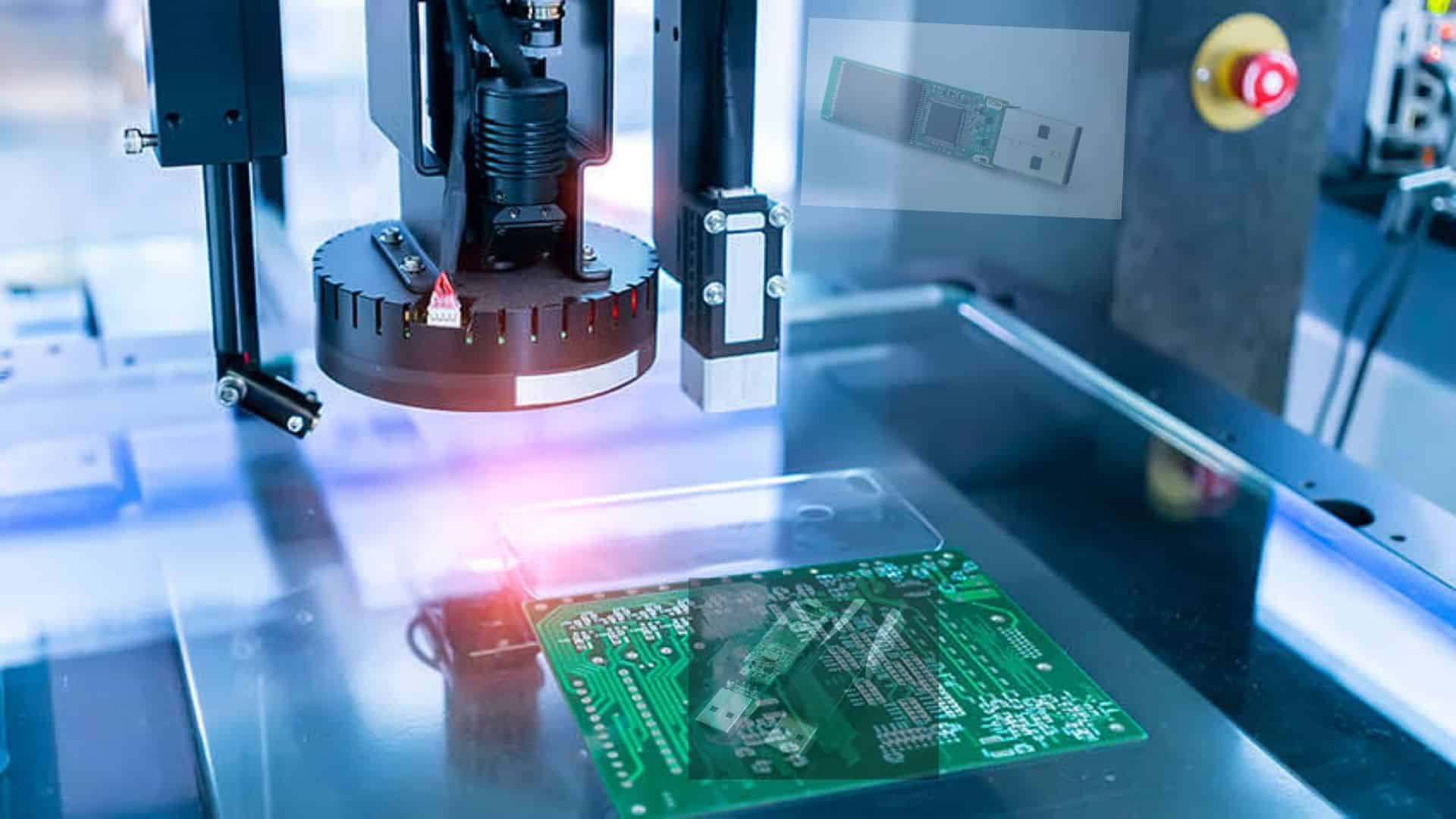
Flash storage has become an essential component in modern digital devices, from smartphones and laptops to external storage solutions. Ensuring the quality and reliability of flash storage products is crucial, particularly for custom made flash drives, personalised thumb drives, and custom USB memory sticks. Quality control (QC) testing plays a vital role in verifying performance, durability, and security, ensuring that these storage devices meet industry standards and consumer expectations.
Why QC Testing Is Crucial in Flash Storage Manufacturing
The demand for high-performance, reliable flash storage continues to grow, making quality control a critical process in manufacturing. Without rigorous testing, flash drives may suffer from:
- Data corruption and loss
- Slow transfer speeds
- Incompatibility with devices
- Shortened lifespan
Manufacturers invest in QC testing to ensure that custom made flash drives and other storage solutions deliver optimal performance and longevity.
Key Stages of QC Testing in Flash Storage Manufacturing
1. Raw Material Inspection
Before production begins, manufacturers must ensure that the raw materials used in personalised thumb drives and custom USB memory sticks meet quality standards. This includes:
- Memory chips: Checking for defects, verifying storage capacity, and assessing read/write speeds.
- USB controllers: Ensuring compatibility with USB 2.0, 3.0, or 3.1 standards.
- Casings and connectors: Testing for durability and resistance to physical damage.
2. Functional Testing
Each flash drive undergoes functional tests to validate its performance. These tests include:
- Read and Write Speed Testing: Ensuring the device meets advertised speeds.
- Device Recognition Testing: Verifying that the flash drive is detected by different operating systems.
- File Transfer Testing: Assessing how efficiently the device handles data movement.
This step is especially important for custom made flash drives, as businesses often require reliable and high-speed data storage for corporate use.
3. Durability and Stress Testing
Flash drives must withstand everyday wear and tear. Stress testing helps determine their durability under extreme conditions, such as:
- Temperature Variations: Testing performance in extreme hot and cold environments.
- Drop and Impact Resistance: Assessing how well the drive survives physical shocks.
- Moisture and Dust Exposure: Ensuring resistance to environmental factors.
4. Data Integrity Testing
A primary concern with flash storage is data retention. Manufacturers conduct tests to ensure stored files remain intact and accessible over time. This includes:
- Bit Error Rate (BER) Testing: Measuring data corruption frequency.
- Endurance Testing: Simulating extensive read/write cycles to predict lifespan.
High-quality personalised thumb drives must retain data integrity, especially when used for business presentations or personal data storage.
5. Compatibility Testing
Not all flash drives work seamlessly across all devices. Compatibility testing ensures that custom USB memory sticks function correctly with various:
- Operating systems (Windows, macOS, Linux, etc.)
- Smart TVs, gaming consoles, and other media devices
- USB ports of different speeds (USB 2.0, USB 3.0, USB-C)
6. Security Testing
Security is a major concern, particularly for custom made flash drives used by businesses or government agencies. Security tests include:
- Encryption Testing: Ensuring built-in encryption functions properly.
- Virus and Malware Checks: Verifying the drive is free from pre-installed threats.
- Password Protection Testing: Assessing the reliability of access control mechanisms.
7. Firmware Testing and Updates
Firmware plays a critical role in the functionality of a flash drive. During QC testing, manufacturers check for:
- Firmware Bugs: Identifying and fixing software issues before distribution.
- Update Mechanisms: Ensuring the firmware can be easily updated without compromising data.
- Security Patches: Protecting against potential cyber threats.
Benefits of Rigorous QC Testing in Flash Storage
1. Enhanced Reliability and Performance
Through QC testing, manufacturers can guarantee that personalised thumb drives meet speed and performance expectations.
2. Reduced Product Failures
By identifying defects early, manufacturers minimize the risk of faulty custom USB memory sticks reaching customers.
3. Customer Satisfaction and Brand Reputation
Consumers and businesses trust brands that consistently deliver high-quality, durable flash storage solutions.
4. Compliance with Industry Standards
QC testing ensures flash drives meet industry regulations such as CE, FCC, and RoHS certifications.
5. Longer Product Lifespan
Well-tested flash drives last longer, providing better value for consumers and reducing electronic waste.
Common QC Testing Challenges and Solutions
1. Counterfeit Components
Fake memory chips can affect performance and lifespan. Solution: Implement strict supplier verification and sourcing policies.
2. Storage Capacity Misrepresentation
Some manufacturers may sell drives with misleading capacity claims. Solution: Use software tools to verify actual storage capacity.
3. Firmware Vulnerabilities
Insecure firmware can expose users to cyber threats. Solution: Regular firmware updates and security patches.
4. Variability in USB Controller Performance
Different controllers can lead to inconsistent read/write speeds. Solution: Standardize on high-quality controllers with proven reliability.
5. Heat and Overuse Damage
Excessive heat generation can shorten the lifespan of flash drives. Solution: Implement thermal testing to ensure safe operation under different workloads.
Future Trends in QC Testing for Flash Storage
1. Artificial Intelligence in Quality Control
AI-powered systems can detect manufacturing defects and optimize testing processes, ensuring higher accuracy and faster QC evaluations.
2. Blockchain for Supply Chain Transparency
Blockchain technology can verify component authenticity and track quality assurance records, reducing the risk of counterfeit parts.
3. Advancements in NAND Flash Technology
As NAND flash technology evolves, QC testing must adapt to ensure optimal performance and longer-lasting storage solutions.
4. Increased Automation in QC Testing
Automated testing tools reduce human error and improve the efficiency of flash storage testing, ensuring better results in less time.
Conclusion
QC testing is an essential step in flash storage manufacturing, ensuring that custom made flash drives, personalised thumb drives, and custom USB memory sticks meet quality, security, and performance standards. Investing in rigorous testing not only protects consumer data but also strengthens brand trust and product reliability in an increasingly digital world. By implementing comprehensive QC procedures, manufacturers can provide high-quality storage solutions that cater to both personal and professional needs.
As technology advances, the role of QC testing will continue to evolve, incorporating new tools and techniques to ensure the highest standards in flash storage manufacturing. Whether for business, personal use, or government applications, a well-tested flash drive remains the key to secure and efficient data storage.